トヨタ自動車 小林様 インタビューその8|資格取得後と、今後の目標とは?
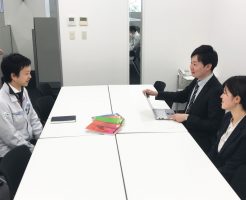
トヨタ自動車 MS組立物流生技部組立SE室 小林 直人様 CPE資格(現在のCPE-B級資格)の資格取得者インタビューをお伺いしました。 (聞き手:日本能率協会 資格制度事務局 勝田 / 中本 / 柏原) ※敬称略 資格・・・
もし、どこかに工場や生産拠点があれば、その製品を“どのようにつくるか”という工程を担う生産技術が必ず存在します。
生産技術分野におけるプロフェッショナルのための資格「CPE資格」試験に準拠した公式ガイド。
生産技術者として必要なマネジメントスキルを体系化しており、理解しやすくなっています。
CPE試験対策や、生産技術業務の知識向上など自己学習にもお役立てください。
※詳しくは「生産技術者マネジメントガイド」詳細をご覧ください。
トヨタ自動車 MS組立物流生技部組立SE室 小林 直人様 CPE資格(現在のCPE-B級資格)の資格取得者インタビューをお伺いしました。 (聞き手:日本能率協会 資格制度事務局 勝田 / 中本 / 柏原) ※敬称略 資格・・・
株式会社堀場製作所 生産本部 生産技術部 生産技術チーム 志村 美代子さんにCPE資格(CPE-B級、CPE-A級)の資格取得者インタビューにご協力いただきました。 (※聞き手 日本能率協会 資格制度事務局 柏原) ※敬・・・
株式会社堀場製作所 生産本部 生産技術部 生産技術チーム 志村 美代子さんにCPE資格(CPE-B級、CPE-A級)の資格取得者インタビューにご協力いただきました。 (※聞き手 日本能率協会 資格制度事務局 柏原) ※敬・・・
トヨタ自動車 MS組立物流生技部組立SE室 小林 直人様 CPE資格(現在のCPE-B級資格)の資格取得者インタビューをお伺いしました。 (聞き手:日本能率協会 資格制度事務局 勝田 / 中本 / 柏原) ※敬称略 CP・・・
株式会社堀場製作所 生産本部 生産技術部 生産技術チーム 志村 美代子さんにCPE資格(CPE-B級、CPE-A級)の資格取得者インタビューにご協力いただきました。 (※聞き手 日本能率協会 資格制度事務局 柏原) ※敬・・・
「堀場製作所 志村様 インタビューその7|A級とB級の難易度について感じたことがあれば教えてください。A級B級で学習方法を変えたなどあればあわせて教えてください。」の続きを読む
トヨタ自動車 MS組立物流生技部組立SE室 小林 直人様 CPE資格(現在のCPE-B級資格)の資格取得者インタビューをお伺いしました。 (聞き手:日本能率協会 資格制度事務局 勝田 / 中本 / 柏原) ※敬称略 CP・・・
株式会社堀場製作所 生産本部 生産技術部 生産技術チーム 志村 美代子さんにCPE資格(CPE-B級、CPE-A級)の資格取得者インタビューにご協力いただきました。 (※聞き手 日本能率協会 資格制度事務局 柏原) ※敬・・・
「堀場製作所 志村様 インタビューその6|B級合格後、A級までチャレンジしようと思った動機(理由)を教えてください。」の続きを読む
株式会社堀場製作所 生産本部 生産技術部 生産技術チーム 志村 美代子さんにCPE資格(CPE-B級、CPE-A級)の資格取得者インタビューにご協力いただきました。 (※聞き手 日本能率協会 資格制度事務局 柏原) ※敬・・・
トヨタ自動車 MS組立物流生技部組立SE室 小林 直人様 CPE資格(現在のCPE-B級資格)の資格取得者インタビューをお伺いしました。 (聞き手:日本能率協会 資格制度事務局 勝田 / 中本 / 柏原) ※敬称略 CP・・・
株式会社堀場製作所 生産本部 生産技術部 生産技術チーム 志村 美代子さんにCPE資格(CPE-B級、CPE-A級)の資格取得者インタビューにご協力いただきました。 (※聞き手 日本能率協会 資格制度事務局 柏原) ※敬・・・
「堀場製作所 志村様 インタビューその4|資格を取得したことで良かったこと、業務に役立ったと感じたことがあれば教えてください。」の続きを読む